Boeing installs engines on 777X flight test aircraft
The aviation industry has been on edge waiting for the Boeing 777X to perform its maiden flight, and with the recent installation of its two enormous engines, this moment is now just around the corner.
Boeing recently published on social media that they have installed the two General Electric GE9X engines to the first flight-test aircraft, not only making it the largest twin ever produced, but outlining the significance of the world’s largest turbofan engine.
Now that’s a big engine! We recently installed both GE9X engines on the first #777X flight test airplane. Designed specifically for the 777X by @GEAviation, the engines have the largest fan ever produced for a commercial jet! Check out some beauty shots of the install. pic.twitter.com/zeLg339yTK
— Boeing Airplanes (@BoeingAirplanes) January 4, 2019
The following image from Jon Ostrower illustrates the size of the engines compared to their predecessors, the GE90-115Bs and the cross-section of a 737 fuselage:
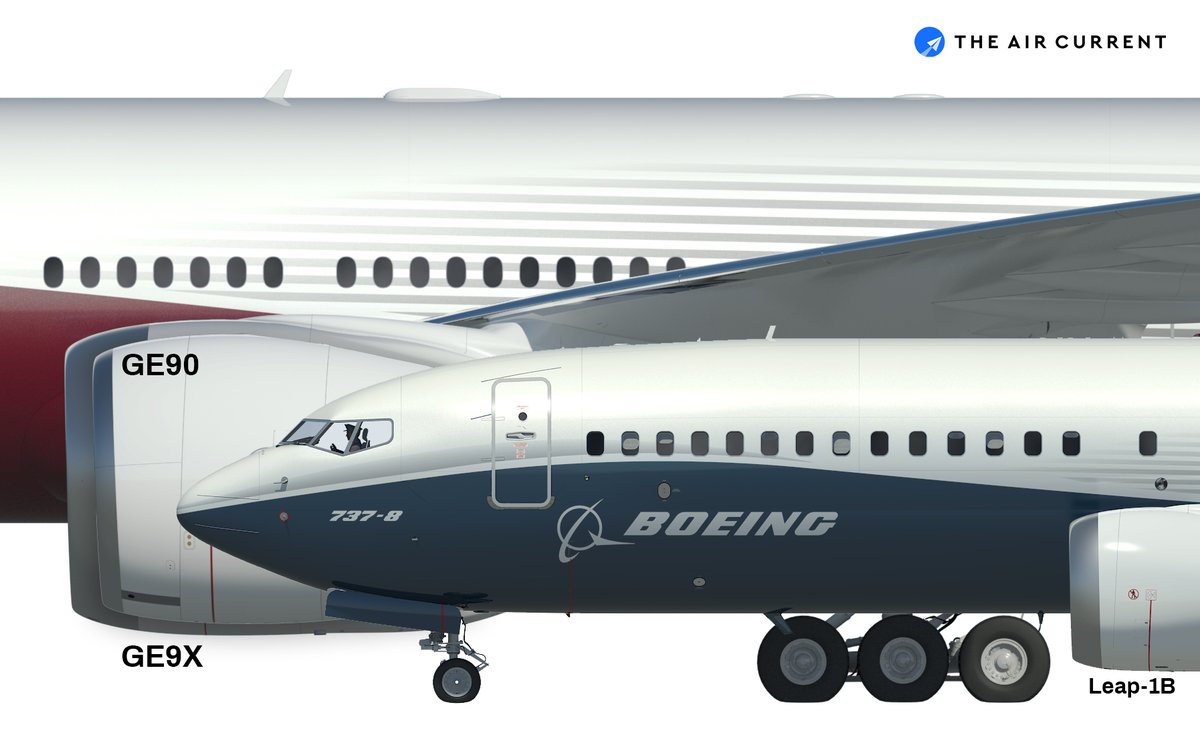
Despite the breathtaking size of the GE9X, the engine is less powerful than the GE90-115B. The revised aerodynamics of the 777X and the larger wing means less thrust is required to get the aircraft in the air.
The following table compares the specifications of the GE90 and GE9X:
Engine | Fan Diameter | Fan Blades | Thrust | Bypass Ratio |
GE90-115B | 330cm (128in) | 22 | 115,540lb | 9:1 |
GE9X-105B1A | 340cm (134in) | 16 | 105,000lb | 10:1 |
The massive fan blades visible are fourth-generation carbon-fiber blades that feed air into an 11-stage high-pressure compressor with a 27:1 pressure ratio, making it the first commercial engine with a pressure-ratio this high according to GE.
Additionally, GE has filled the engine with parts that are made using additive manufacturing (commonly known as 3D printing), allowing for complex and durable parts to be produced at a lower price. GE states that some parts that were previously impossible to build can now be produced using additive manufacturing.
Ceramic Matrix Composites (CMCs) play a large role in the efficiency of this engine because of their ability to withstand greater temperatures than metals used in older engines. Installed in the combustor and turbine, the engine is able to operate at greater temperatures, reducing fuel burn.
GE released this video which breaks down the engine in greater depth:
Now installed, Boeing will continue to work on the aircraft, preparing the systems and verifying construction was completed correctly, before towing it out of the hangar for painting, engine runs, ground testing and then finally, first flight, which is expected during the second quarter of this year.
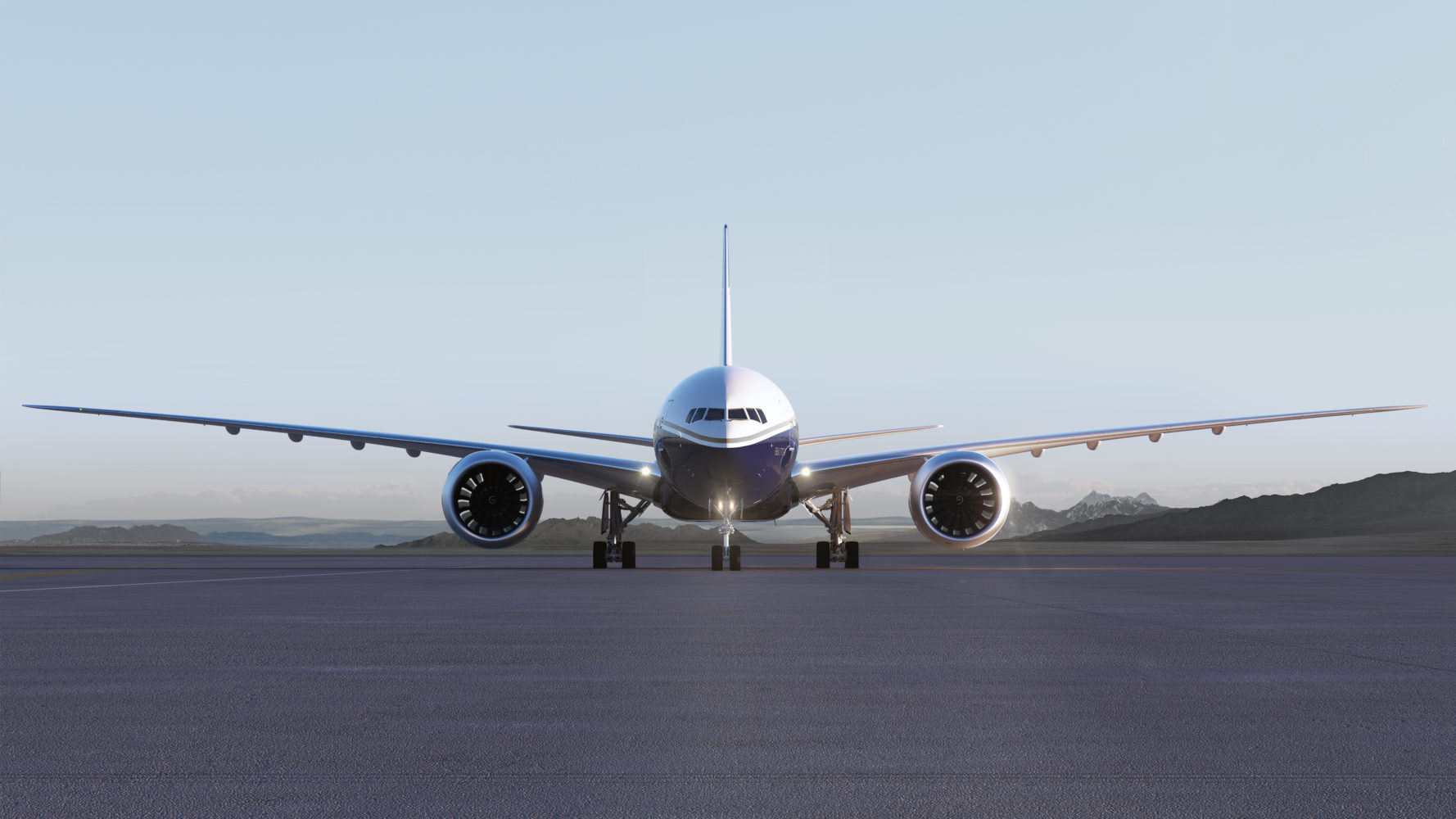
For those that haven’t heard the GE9X, here is a video from GE Aviation that demonstrates the engine running at a high-power setting during ground runs. GE states the engine is the quietest ever produced by the company and will be quieter than the GEnx on the Boeing 787 Dreamliner.
GE will be the only engine supplier for the 777X Family, with the GE9X covering all variants, similar to how Rolls-Royce is the exclusive engine supplier for the A350 and A330neo.