The Federal Aviation Administration (FAA) has issued a new airworthiness directive (AD) for the Pratt & Whitney engines that power the Airbus A220 and Embraer E2 190/95, following the two recent in-flight shutdowns involving the PW1524G-3 engine.
This AD requires initial and repetitive borescope inspections of the low-pressure compressor (LPC) inlet guide vane (IGV) and the LPC rotor 1 (R1) and, depending on the results of the inspections, a possible replacement of the LPC.
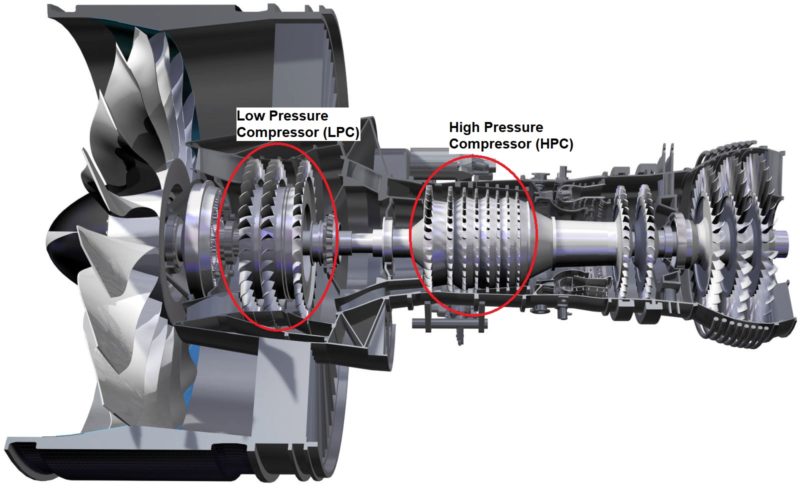
What is the Problem With These Engines?
These inspections are an evolution of the regime implemented after two recent in-flight shutdowns (IFSDs). Both IFSDs occurred with the same airline, aircraft type and route – Swiss A220-300 operating the route Geneva International Airport to London Heathrow. The first incident happened on 25th July and the second one on 16th September.
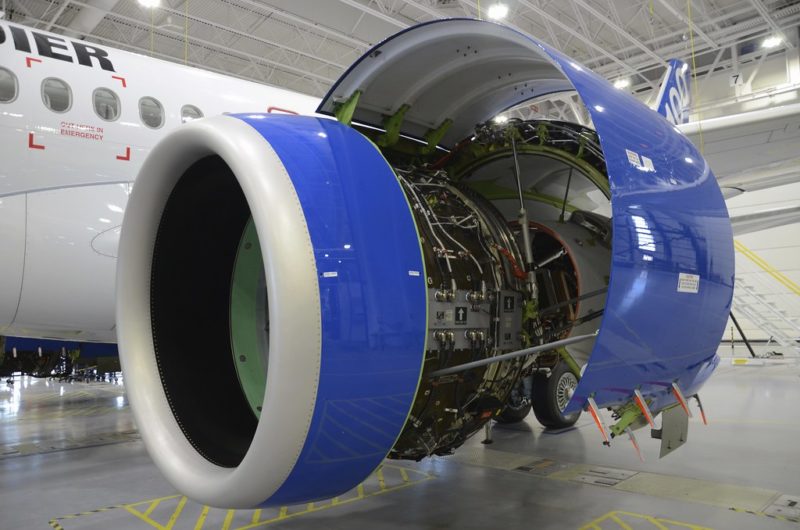
A post-flight examination was made on both incidents, on the first one the low-pressure compressor rotor stage 1 was missing from the engine. On the second incident, a hole on the LPC case and a separated low pressure compressor stage 1 rotor were found.
The incidents’ similarities extend beyond the operator and equipment types. Both occurred as the flights were approaching cruise altitude – the first one at FL350 and the second at FL320. According to FAA, each engine had fewer than 300 cycles – the first engine failed at 154 cycles, while the second had 230 cycles.
“Both failures of the LPC R1 occurred at low flight cycles since new,” the FAA said. “The manufacturer has recommended that these inspections occur within the next 50 flight cycles and the FAA has adopted that recommendation. Based on current operational usage of the affected airplanes, 50 flight cycles equates to approximately 7 to 10 operating days. Therefore, the FAA has determined that low flight-cycle rotors require inspections within the next 50 flight cycles from the effective date of this AD to prevent LPC R1 failures.”
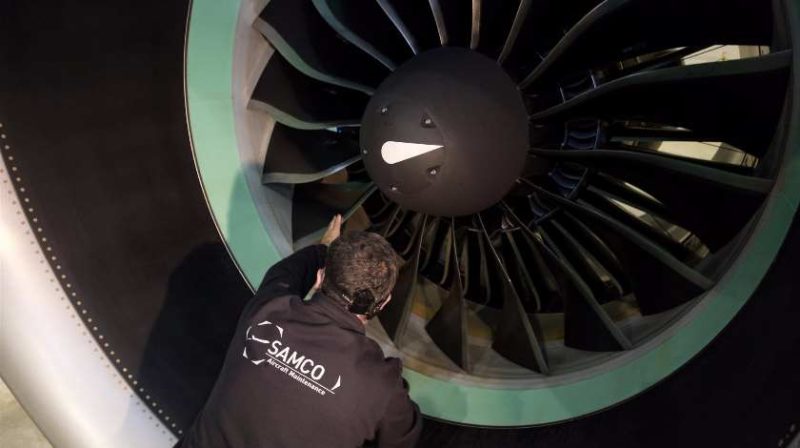
If inspections turn up rotor cracks or damage that “exceeds serviceable damage” or misaligned guide vanes the LPC must be replaced. Repetitive checks must be done every 50 cycles until the engine surpasses 300 cycles.
This unsafe condition, if not addressed, could result in the uncontained release of the LPC R1, in-flight shutdown, causing damages to the engine and consequential damages to the airplane.
The airworthiness directive was published on 26th September and effective immediately.
Costs
For the airlines that operate airplanes with these engines, the cost per product may be significant if the LPC needs to be replaced.
For the borescope inspection per inspection cycle, the FAA estimates 4 work-hours plus a part cost of $340 bringing the total of $6,120. However if the company needs to replace the LPC it will be much more expensive, the FAA estimates 40 work-hours ($85 per hour) plus a part cost of $156,000 making for a total of $159,400.
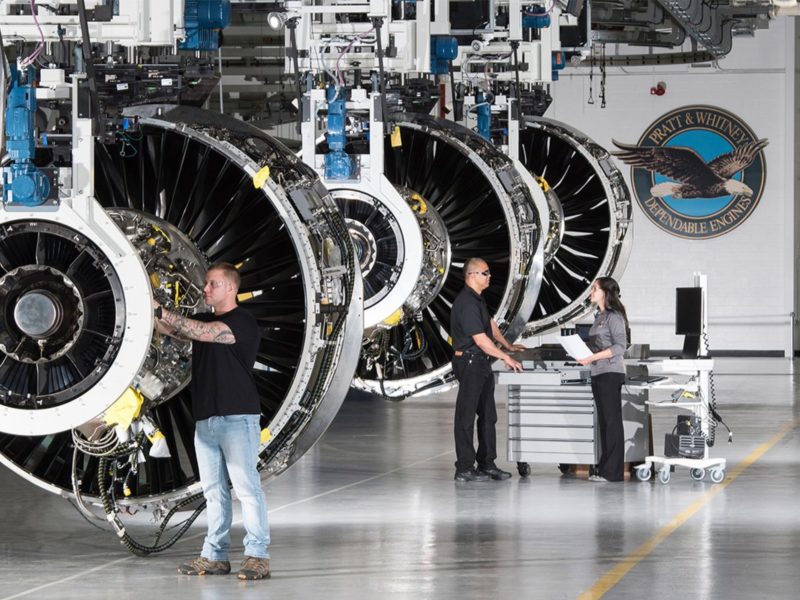
The FAA also estimates that this AD affects 18 engines installed on airplanes of U.S. registry.
This directive is valid for all Pratt & Whitney Models PW1519G, PW1521G, PW1521GA, PW1524G, PW1525G, PW1521G-3, PW1524G-3, PW1525G-3, PW1919G, PW1921G, PW1922G, PW1923G and PW1923G-A turbofan engines that have accumulated fewer than 300 flight cycles.
Although these IFSDs occurred on the PW1524G-3 model turbofan engines, the FAA is including PW1900 engines in the applicability of the AD; due to similarities in type design that makes these engines susceptible to the same unsafe conditions.
Previous Problems
It is the second time that these engines have received an AD from FAA, the first one was prompted by corrosion found on the high-pressure compressor (HPC) front hub; this could result in certain HPC front hubs cracking before reaching their published life limit.
For those interested in additional details, here is the article: