The Federal Aviation Administration (FAA) has issued two new airworthiness directives (AD) regarding the Boeing 737 MAX, one for an electrical grounding issue and one for LEAP-1B engine corrosion reports.
Electrical Grounding Issue
At the beginning of April airlines pulled dozens of 737 MAX aircraft from service; this was after Boeing warned of a production-related electrical grounding problem in a backup power control unit, situated in the cockpit on some recently built airplanes. The FAA was advised by the manufacturer “that its design changes to the referenced panel assemblies had created an urgent safety issue”.
According to the FAA, this new AD was prompted by manufacturing design changes to certain metallic support panel assemblies installed in the flight deck. The design changes resulted in poor bonding of the panel assemblies, consequently leading to insufficient electrical grounding in the installed equipment. Degradation of bonds essential for the electrical grounding of equipment could affect the operation of certain systems, including engine ice protection.
“We continue to work closely with the FAA and our customers to address the ground path issue in affected 737s.”
a Boeing spokeswoman said to Reuters
The FAA has explained that this issue was discovered during testing of a newly manufactured Boeing Model 737-8 airplane. During testing the electrical power systems did not perform as expected; this behaviour was also observed in two other places, including the mounting tray for the standby power control unit (SPCU), which is located behind the first officer, and the main instrument panel (MIP) assembly, which is located in front of and between the captain and first officer.
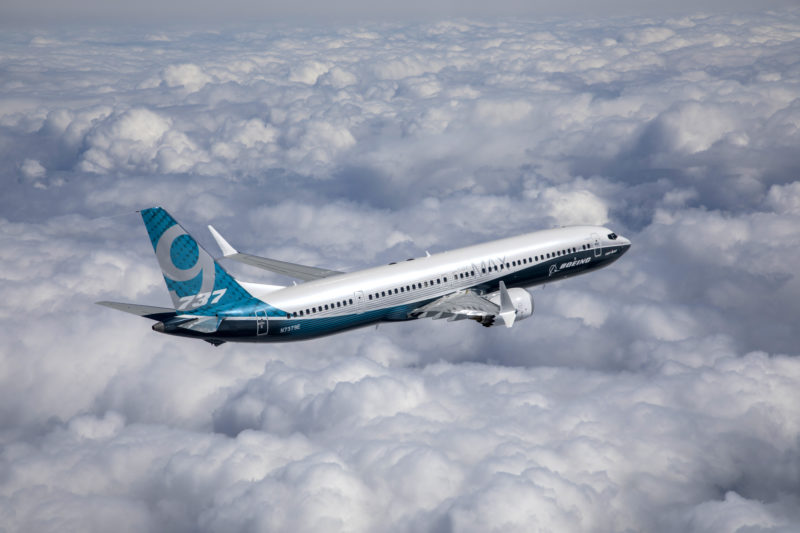
Required Actions
In order to address this issue, the AD requires modifying the electrical bonding of certain support panel assemblies; these panels are installed to provide sufficient electrical grounding for the equipment in the flight deck.
Boeing is currently developing service information for a modification that will address this unsafe condition.
The FAA says that 71 737-8 and 737-9 planes with US registration are affected by this AD, but sources have said to Reuters that it actually impacts more than 300 planes in Boeing’s inventory. To comply with these actions, the US authority estimates that 68 airplanes will need to have multiple flight deck panels modified. This is estimated to take around 24 work-hours, at a cost of $85 per hour with a part cost of $200; each aircraft will subsequently cost approximately $2,240 but, once the inspection is mandatory, this will mean that there will be a total spend by US operators of $152,320.
Another 3 aircraft have to modify one flight deck panel, taking around nine work-hours with a part cost of $100; each aircraft will subsequently cost approximately $865, with a total cost for all airlines of $2,595.
If this situation if not addressed it could result in the loss of critical functions and/or multiple simultaneous flight deck effects, which may prevent continued safe flight and landing.
“All affected airplanes, both in the US and worldwide, have been removed from service, pending development and implementation of approved corrective action that will address the unsafe condition.”
This AD is effective from April 30th 2021 and special flights are permitted to operate the airplane to a location where the airplane can be modified.
Engine Corrosion Reports
The worldwide fleet of the 737 MAX was grounded for more than two years, mainly in dry places like deserts; this was done to preserve the aircraft in almost ideal conditions, but some parts might now be showing some wear and tear. This second AD was prompted by multiple reports of pressure sub-system (PSS) unit faults, due to pressure transducer corrosion following extended storage periods.
The manufacturer’s investigation found that certain PSS units, identified by serial number, have been exposed to conditions that make pressure transducers in these units susceptible to an increased rate of faults. These conditions include moisture ingress from long-term on-wing storage, coupled with certain manufacturing processes of the affected pressure transducers. Together these conditions can cause corrosion and subsequent electrical shorting of the pins in the pressure transducer.
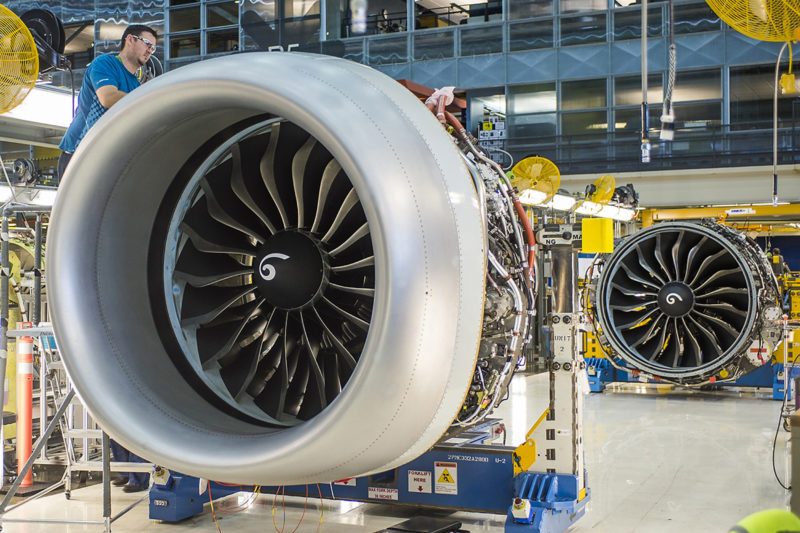
“In April 2021 the FAA received a report from CFM, the engine manufacturer, of numerous instances of PSS unit faults. The manufacturer reported that these faults have been occurring since October 2020 and are a result of pressure transducer corrosion following extended storage periods. The manufacturer’s investigation found that certain PSS units, identified by serial number, have been exposed to conditions that make pressure transducers in these units susceptible to an increased rate of faults.”
To resolve this issue the FAA has presented three scenarios for airlines: For an engine in service, this AD requires checks for engine maintenance messages, related to the pressure transducer, and, depending on the results of the check, replacement of the PSS unit before further flight. For engines with fewer than 15 hours of electrical power applied to the PSS unit, within the past 90 days, and for an engine that is not in service, this AD requires applying electrical power to the PSS unit before further flight.
The FAA estimates that this AD affects 158 engines installed on airplanes of US registry; if not addressed this condition could result in the loss of engine thrust control and reduced control of the airplane.